Printed circuit boards (PCBs) form the backbone of every electronic device, and at the heart of every PCB lies the substrate material. Choosing the right PCB substrate material is crucial for ensuring the electrical performance, mechanical stability, and overall reliability of a device. Whether you are building a simple consumer gadget or a complex high-frequency communication device, the choice between FR4, Polyimide, and Rogers materials can make a significant difference.
Understanding the differences in PCB substrate materials is essential for effective circuit performance and cost control.
This guide will help you understand the core properties of these materials and support you in making an informed decision for your next project.
Why PCB Substrate Matters for Your Circuit Design?
The PCB substrate material determines several important parameters, including dielectric constant, thermal performance, flexibility, and cost. The choice impacts signal speed, temperature tolerance, and even product lifespan. A poor selection can lead to electrical failure or inefficiencies, especially in high-frequency PCB materials applications.
Considering dielectric constant PCB values, thermal resilience, and flexibility early in the design phase leads to better long-term outcomes.
FR4: The Standard Go-To for Most Applications
FR4, a fiberglass-reinforced epoxy laminate, is the most widely used PCB substrate material due to its balance of cost, performance, and availability. It offers a dielectric constant of around 4.5, providing stable electrical performance for general-purpose designs. Known for its good mechanical strength and adequate thermal resistance (~130°C to 140°C Tg), FR4 provides sufficient durability for most commercial and industrial products. It is easy to fabricate, compatible with standard manufacturing processes, and offers a reliable baseline for low- to medium-frequency applications. However, FR4 may not be suitable for very high-frequency PCB materials or extremely high-temperature environments.
Key Properties:
· Dielectric constant: ~4.5
· Good mechanical strength
· Adequate thermal resistance (~130°C to 140°C Tg)
· Affordable and easily manufacturable
Use Cases:
· Consumer electronics
· Industrial control systems
· Automotive electronics (standard segments)
FR4 is ideal for designs where high-frequency performance and extreme thermal endurance are not critical.
Polyimide: For Flexibility and Thermal Resilience
Polyimide substrates offer superior thermal stability and mechanical flexibility, making them indispensable for flex PCB substrate India manufacturing and applications operating in harsh environments. With a dielectric constant typically ranging from 3.2 to 3.5, polyimide materials provide excellent electrical performance even under extreme mechanical stress or elevated temperatures. They are highly resistant to chemicals, radiation, and humidity, making them a durable choice for demanding environments.
When it comes to thermal PCB material selection, polyimide consistently outperforms traditional options, especially in mission-critical applications requiring durability and heat resistance.
Key Properties:
· Dielectric constant: ~3.2 to 3.5
· High thermal endurance (up to 260°C or higher)
· Excellent mechanical durability
· Good chemical resistance
Use Cases:
· Flexible circuits and dynamic bending applications
· Aerospace and military systems
· Automotive engine control modules
Polyimide is the preferred choice when designing for environments requiring superior thermal resilience and mechanical flexibility.
Rogers: Ideal for High-Frequency and RF Circuits
Rogers materials are specifically engineered for high-performance applications requiring minimal signal loss and stable dielectric properties across frequencies. Offering dielectric constants ranging from 2.2 to 10.2, Rogers substrates allow design flexibility for microwave, RF, and high-speed digital circuits. They exhibit extremely low dissipation factors, ensuring high signal integrity even at very high frequencies.
Choosing Rogers material PCB India solutions enables companies to meet demanding performance requirements, especially in the telecom, defense, and aerospace sectors.
Key Properties:
· Dielectric constant: 2.2 to 10.2 (depending on the grade)
· Extremely low signal loss
· Excellent thermal management
· Higher material cost compared to FR4
Use Cases:
· RF and microwave communications
· Satellite and radar systems
· 5G infrastructure
When dealing with high-frequency PCB materials, Rogers substrates deliver unmatched signal integrity and consistency, crucial for communication and aerospace industries.
Substrate Comparison Chart
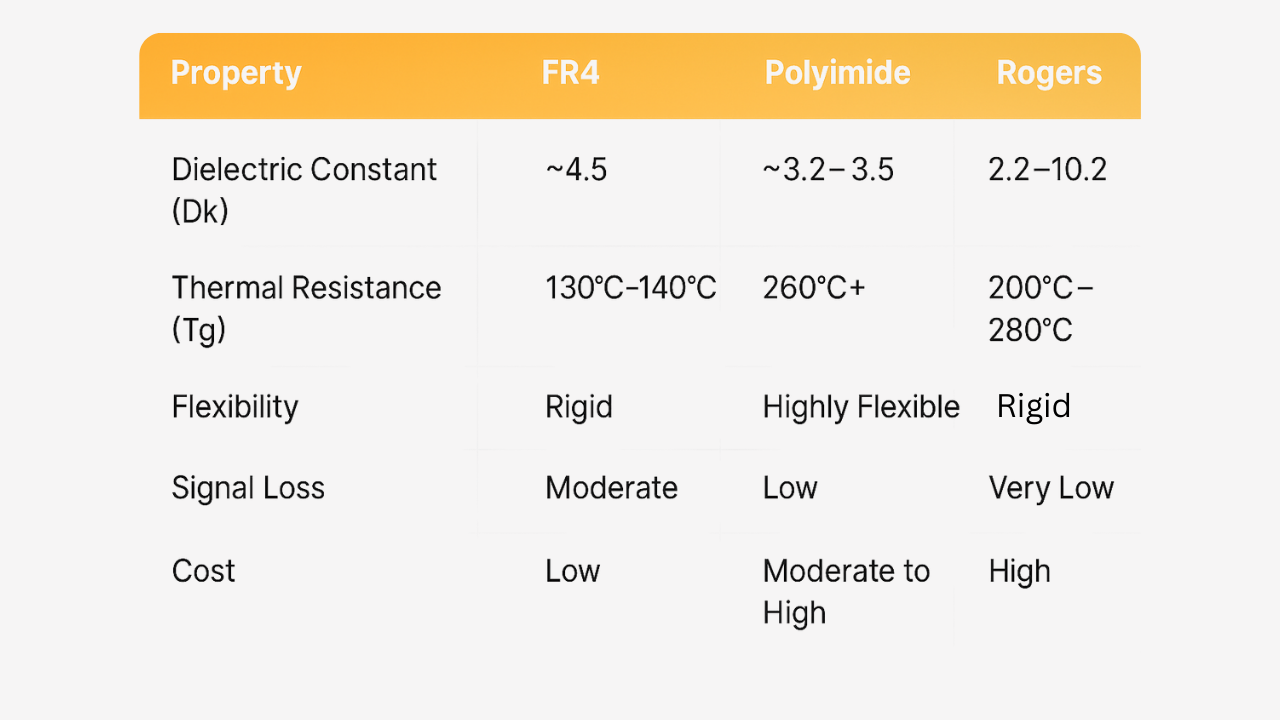
This PCB substrate comparison highlights how each material type matches different performance and budgetary needs.
Which Material Suits Which Industry/Application?
Checklist: How to Pick the Right PCB Substrate?
When selecting between FR4, Polyimide, or Rogers, consider the following:
· Operating Frequency: For RF/high-frequency, prioritize Rogers.
· Thermal Environment: For high heat exposure, opt for Polyimide.
· Mechanical Requirements: Need flexibility? Polyimide is key.
· Budget Constraints: For cost-sensitive projects, FR4 suffices.
· Reliability and Lifespan: High-reliability applications favor Polyimide or Rogers.
Considering factors like dielectric constant PCB stability and thermal PCB material selection early helps engineers avoid costly redesigns later.
How LionCircuits Supports Multi-Material PCB Fabrication?
LionCircuits brings extensive experience in fabricating PCBs across a wide range of materials, including FR4, Polyimide, and Rogers. Our expertise in handling diverse PCB substrate materials ensures that customers can match their design needs with the right material properties for optimal performance.
With a focus on precision manufacturing and material reliability, we help support projects across industries such as consumer electronics, automotive, aerospace, and telecommunications. Our streamlined platform simplifies the process — from material selection to quoting and production — making it easier for hardware teams to realize high-quality, application-specific PCB designs.
Whether you need a flex PCB substrate India build, Rogers material PCB India solution for RF circuits, or a standard FR4 vs Polyimide vs Rogers comparison for an industrial application, LionCircuits ensures high quality, dependable multi-material PCB solutions tailored to your needs.
Conclusion
Selecting the appropriate PCB substrate material—whether FR4, Polyimide, or Rogers—is a strategic decision that impacts every aspect of your electronic product’s performance and lifespan.
By understanding the advantages of each material and applying a careful PCB substrate comparison, engineers can optimize their designs for electrical performance, thermal durability, and mechanical resilience.
Get in touch with LionCircuits for expert guidance and seamless multi-material PCB fabrication to bring your designs to life.